

You'll want to delete the code already saved under probe commands and paste/type the following: Just open Candle, click the " Service" Toolbar and select " Settings". To configure Candle for the use of your Z Probe, you do not need your CNC to be connected to the computer. Make sure to keep this number handy for the next step. While we manufacture our probes to be as consistent as possible to bring you the best experience, inconsistencies can happen, so it is important for you to measure your specific probes height/thickness. When not in use, you can even wrap the wire around the X axis stepper motor a few times to make it is not in the way when actively working on projects. The best way to do this is to take the other end of the Z Probe not connected to the board, and bring it around and to the left of your CNC.
CNC USB CONTROLLER SET Z HEIGHT HOW TO
Since you are going to be working with the CNC from the front, with this board facing away, it's best to consider how to bring the probe to you for easy use in the future. While the entire process isn't too difficult, this is definitely the easy part! The image below shows out 3018-PROVer CNC controller board. How do I Set It Up? Part 1: Probe Installation Once you've used one, you'll never want to go back to the old method. True Z-0 = (Stock/Base Z-0) - Base thicknessĪnd there you have it, the true value of a Z Probe. Since the base is a known quantity as a manufactured product, you can pre-program your CNC to know the exact thickness of your probe base (measuring it with calipers) and forever afterwards you can achieve setting Z -0 with a press of a button as the CNC uses the following formula:

Your CNC knows the exact moment this circuit is created and, along with some simple programming, lets you know a very accurate Z-0 for the stock material combined with the probe base on top of it. They are connected in such a way to your CNC that when the alligator clip (or something conductive it's attached to) touches the base, a circuit is made. The Z Probe is made from two components: A base which is connected to a black wire, and an alligator clip which is connected to a red wire. It's the kind of thing that's hard to teach because you can only know and remember the right "feeling" through practice and experience. There are a lot of different level of the bit pinching your paper, ranging between too little, just right, and too much. Those familiar with 3D printers will probably be familiar with this process and know that using this method is as much of an art as it is a science. At that point you can tell the CNC that the current location is Z-0 = current location - thickness of paper used.
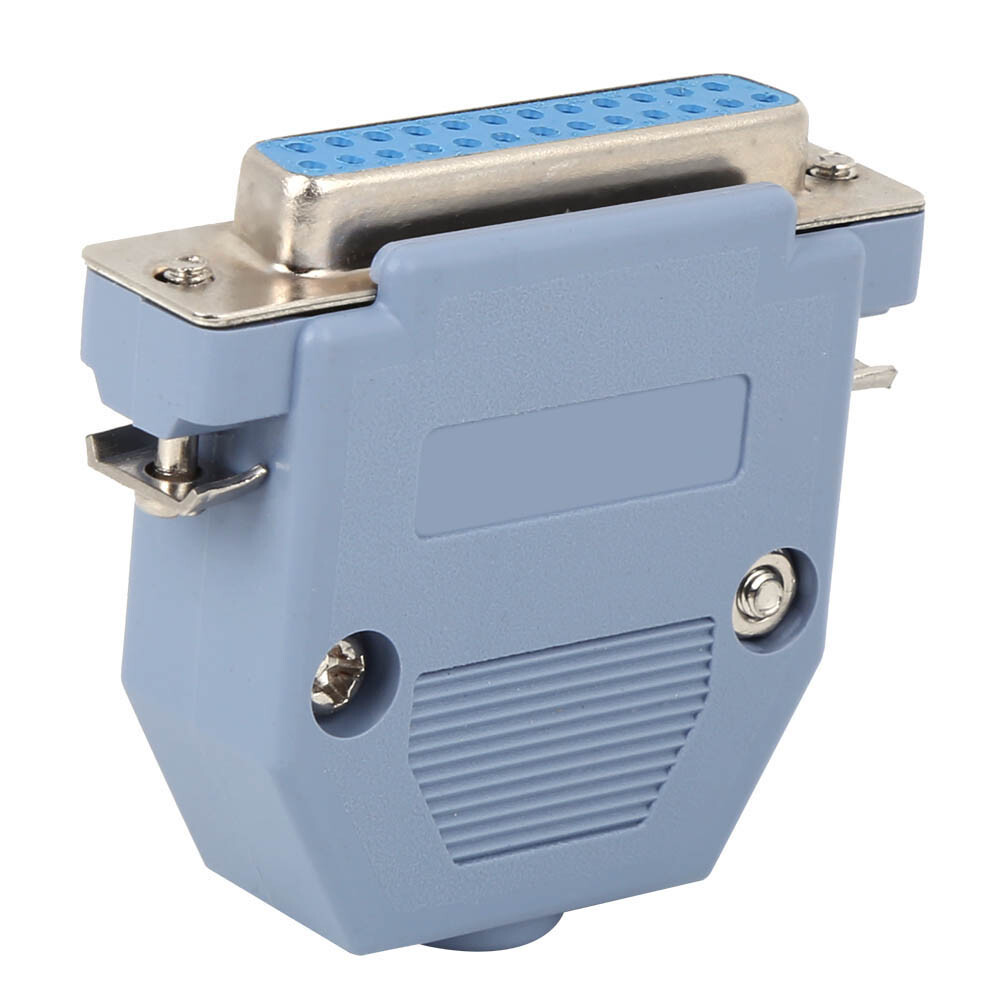
By sliding this back and forth along the surface of your stock material while lowering the Z axis very slowly, you could teach yourself to feel when the tip of your end mill would start to pinch the paper to the stock ever so slightly. Historically, CNC operators would use a thin piece of paper or a feeler gauge.

Obtaining the stock thickness is easy enough, you just use a caliper or similar measuring device to get a measurement, but the Z-0 point can be tricky. Having trouble visualizing? Take a look at this image: By knowing this point as accurately as possible, as well as the exact thickness of your stock material, you are able to fully define your workspace. When you are running any project on your CNC, it is vital for a successful outcome that you carefully define the point at which Z=0.įor most projects, Z-0 is the location on the Z axis of your CNC where the tip of your end mill is flush, or just touching the surface of your stock material.
